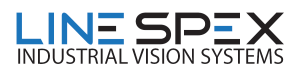
5 Proven Ways to Reduce Downtime
Choose Adequate Equipment
When purchasing or assigning new equipment, it is important to ensure the equipment you choose can handle the size of the load, line speed, and strain it will be under. Some managers may be tempted to use smaller or cheaper equipment to save money upfront and ignore the Total Cost of Ownership (TCO) of running the equipment. Circumstantially, the higher upfront cost of a certain machine is the most cost-efficient option when considering downtime, maintenance costs, total output, and defective rate of your product. When calculating TCO, remember to include direct and indirect costs (such as lifespan, machine efficiency, setup costs, training costs, maintenance needs, and estimated downtime).
Measure Measure Measure
One of the biggest metrics to measure in the manufacturing is Overall Equipment Efficiency (OEE). Once you track your OEE, you can take actionable steps to improve it. There are three major ways to increase your OEE: reduce stops (increase uptime), increase speed (performance), and reduce defects (quality).
To track your OEE, you want to measure the following:
Uptime/Downtime: A ratio of actual uptime to the allotted time the machine was scheduled to run
Speed Loss: How often the machine isn’t running at the optimal/desired speed
Quality Loss: The percentage of defects in the production process (products that do not pass inspection).
After measuring the above three, you will be able to decide which one (or more) need to be addressed.
Stop Firefighting
Reactive approaches are not intuitive. Proactively reducing inefficiencies (preventative & predictive maintenance) are being implemented globally, and for a good reason. Waiting for a machine to stop before replacing something (or conducting maintenance) won’t prevent that issue from happening in the future. Additionally, it is much more inconvenient and costly to relocate personnel or resources to fix an issue at the drop of a pin. This is also known as ‘firefighting’. This duct-tape approach is not sustainable.
We can avoid this by adopting methods of preventative maintenance. Scheduling a time to inspect the machine’s parts and condition, cleaning, lubricating, calibrating, etc. can go a long way. You don’t wait until your engine is smoking before replacing your engine oil – this is the same concept. If you need assistance deciding when to do such maintenance, the owner’s manual is a good place to start. Reaching out to the machine manufacturer is also a good avenue to learn more. Lastly, sharing best practices with colleagues and other facilities within your organization can create a successful learning process for all those involved.
Calculate Dollar Cost of Downtime
Calculating the true cost of downtime should include value of product loss, minutes (or hours) spent reallocating personnel and the cost of the repair.
This provides a true figure of what unplanned production stops are costing per minute to calculate what is a feasible expense when evaluating solutions (such as new software or technology). New additions to your technology mix should reduce enough cost to pay for themselves within a feasible period. When calculating the return on investment, this is referred to as ‘payback period’.
Communication
Keeping open communication between the machine operators and supervisors/managers is crucial for efficiency. The most successful processes are when the machine operators have a thorough understanding about the relationship between downtime and business profits. This makes operators understand that they play an important role in the success of the process and adds purpose to their tasks.
Two workers were hammering on a piece of granite with a sledgehammer. When asked what he was doing, the first worker said, “I’m trying to crack this granite.” When asked the same question, the second worker said, “I’m part of a team building a cathedral.”
~ Ken Blanchard & Donald Carew